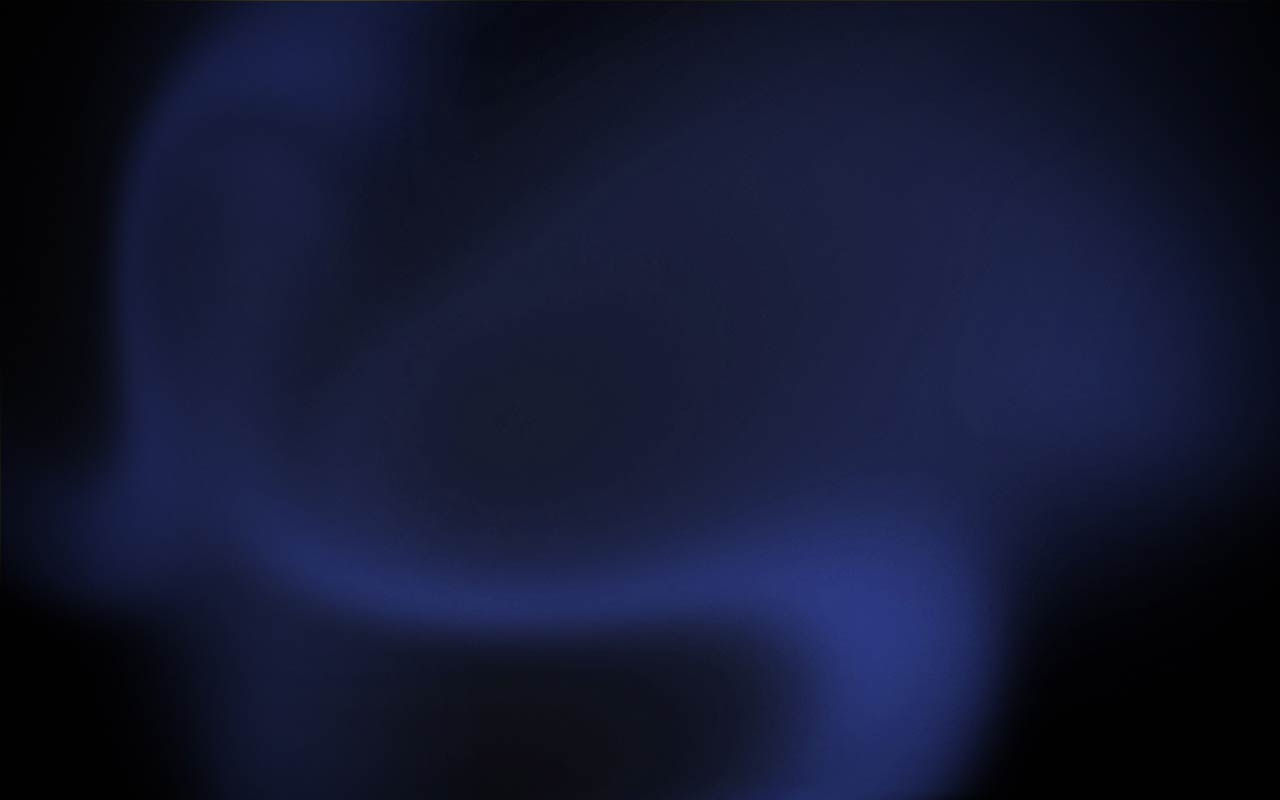
Technical Training
​
When implementing these tools, it is not necessary, under most circumstances, to do a cultural analysis. However, these tools can not be implemented in a vacuum. For instance, as a minimum skills training, on-going support plus management’s direct involvement will be needed. The specific areas of technical skills include the following:
​
​
Statistical Process Control
We are experts in this field and can show you how to use this skill alone to make huge process and financial gains. Whether you want to learn how to do only control charting or all 7 of Ishikawa’s tools, we can show you the ins and outs of SPC. This is a powerful tool set to have and can be used to make huge financial gains. In addition, SPC and MSA are skill sets that should be in place to effectively implement a Lean Initiative.
Measurement System Analysis
This much ignored field is an extremely ripe area to make progress. For example, using these techniques we showed an electronics firm how to save $200,000 by not purchasing new Final Testers. Rather we debottlenecked the existing units and not only deferred the purchase of new testers but also increased line capacity by over 27%. Using this technique alone, we have assisted Plastic Injection molders to increase process capabilities from Cpk of 0.4 to Cpks of over 3. We have a great deal of experience in this field and MSA can be a very effective money making tool for your business.
Designs of Experiments
Skills in DOE are powerful techniques to use at the design, system or process level of a business. They are great at finding ways to reduce variation or new optimal process settings. Our approach emphasizes Classical techniques as we find them to be the most effective although we do teach Taguchi methods as well. There is a tool set known as Shainin techniques which are often referred to while discussing DOE. These techniques are not really designed experiments but rather are an organized set of techniques which focus on variation reduction and are most applicable in the manufacture of discrete components. These techniques are easily learned and, in the correct environment, powerful. We can train you on these and assist you in their application.
​
Quality in Education and Training
Most companies and even most educational institutes do not have a statistical method in place to determine if they have a stable, capable process to educate their students and trainees. Yet no problem is as pervasive as inadequate training in industry. It is the most frequent cause of scrap and rejects, yet in our experience we have found the training system, not the student, is deficient over 85% of the time. Once it is accepted that education and training are processes then the tools of SPC can be applied to assess a variety of topics. For example; it is possible to find where training is inadequate and needs to be bolstered to meet the needs of the business; also it is possible to find where too much training is being done and your company is wasting money; in addition you can statistically validate where it is not practical to train specific individuals and they should be assigned to more appropriate work. All of this can be easily done if you know the techniques.
​
Hoshin-Kanri Planning
Sometimes called Policy Deployment, H-K Planning is a powerful tool to create goals that are supportable by the entire business, top to bottom, and throughout all functional areas. Properly implemented, there is no technique stronger in “getting everyone to sing from the same hymnal”. This is a powerful cultural change agent and must be approached with caution. It also is a much slower, although more effective technique than the Annual Goal and Objectives setting so frequently done in business.
​
Advanced Facilitation Skills
The heart and soul of most business cultures is the business meeting. Yet most meetings are poorly run with inadequate thought given to both the content and the process of the meeting. However, the largest problem is that, if any decisions are reached at all, they often are not supported by those who attended. Consequently, although much time is spent in business meetings, it is largely wasted; frequently, this it due to poor facilitation. The techniques to run an efficient, effective meeting can be taught and learned and we can show you how to use these techniques to achieve major productivity improvements at the Managerial level.
​
Cross-Functional Problem Solving Teams
Learning how to solve tough problems using teams is a necessity in today’s environment. Whether you use the AIAG’s 8D process or some other method such as Ford’s TOPS, problems solved in this fashion are more likely to stay solved. This training combines many of the skills taught in Six Sigma and Advanced Facilitation as well.
​
Customer Satisfaction Surveys
Developing and executing a Survey of this nature is difficult. In spite of this, many firms can create a survey which will elicit the data needed to better satisfy your customer. The problem then becomes how to best analyze these data. When the analysis is in the form of pie charts and Pareto analyses, the benefits of the survey are lost. To be effective a full statistical analysis must be done and we are experts at that technique. This statistical analysis then allows you to “separate the signals from the noise” just like is done in your industrial processes.
​
Employee Attitude Surveys
These are a refinement of the Customer Satisfaction Survey, and like it, we do a complete and thorough statistical analysis so you can proceed with confidence on corrective actions. In so doing it is possible to highlight the issues that are affecting employee’s ability to focus on the work at hand. Once highlighted, these problems can be addressed and corrected. This survey is frequently used in cultural assessments.
